Liquid Membranes
Industrial Liquid Membrane Systems, Replacement and Retrofits
FMT Will Supply Improved Membrane Pre-Treatment to Improve your Membrane Efficiency. FMT Also Supplies And Coordinates Work With Your Current Membrane Provider To Reduce Downtime, Stabilize Flux Rates, Reduce Cleaning Chemical Requirements & Cleaning Cycles, and Extend Membrane Life. FMT Will Recommend Updated Membrane Technologies and Suppliers That Meet Your Current Needs.
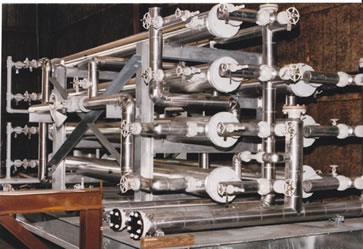
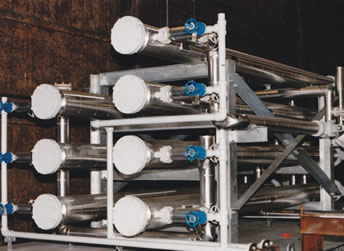
Reverse Osmosis (RO) systems are used for boiler feed water treatment and a host of pharmaceutical, municipal, and other industrial applications. The membrane RO systems are sensitive to contaminants and usually have a pre-filter to protect them. However, the pre-filter is usually designed as an afterthought instead of as the critical protection device it actually is. Pretreatment can include more than just absolute filtration including separation processes such as sedimentation, flotation, granular media, pre-coat filters (DE filters) and screening. Pretreatment problems may include hydrocarbons, Natural Oils, Cryptosporidium & Giardia, fresh & seawater mussels, and mollusks in their various life forms.
Inlet water quality is a moving target, constantly changing and subject to major changes such as construction projects upstream or runoff changes, dredging operations, requirements to totally change feed sources due to aquifer or drought issues. Large surface area filters now exist with small footprints where the efficiency and changes in water source quality can be handled best if considered in the design stage. (See: Industry challenges in water pre-filtration-AFS 2008).
Filters used in refineries and petrochemical plants handle very large volumes of product or processing fluids on a continuous basis. Other plant operations are batch found throughout the process industries. Regardless of whether the process is batch or continuous, on-line time is extremely critical to optimize profitability. Shutting down due to a filtration problem (or any problem) affects bottom line production income by as much as $10,000 per hour or more. Batch operations have more flexibility, but the choice of the filter, its efficiency to perform the required task, and its dirt holding capacity is also a major concern. Potential product sitting in holding tanks that cannot be shipped because the filtrate does not meet Quality Control Specifications can halt production just as in a continuous process.
What do we need from you? Process data and a description of your problem will help. The following form will act as guide.
Filtration & Membrane Technology, Inc.•370 Camden Hills W., Montgomery, TX, 77356•Phone: 713-870-1120